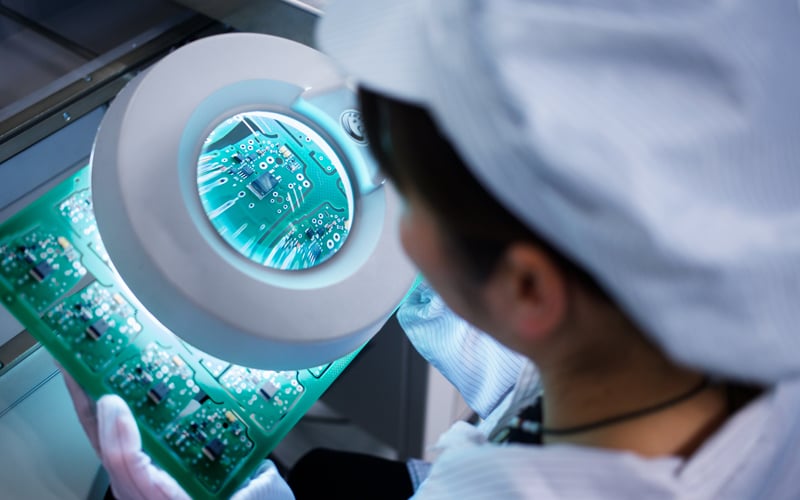
PETALING JAYA: When finance executive Liew (not his real name) was asked to “help out” on the factory floor, he thought it was a bizarre, one-off request. Now, it’s the norm.
Like other multinationals in Malaysia, production and sales at Liew’s company have been throttled by the country’s epic labour crunch, forcing management to increasingly rely upon executives like Liew.
“It has become a norm for me to be called in, to pull up my sleeves and sort out the different parts ejected by the robots in factories whenever production requires. This also happens on weekends,” he told FMT.
Senior management has not been spared. Down the production line, Liew’s colleague, a sales general manager, has been roped in to pack products in boxes for distribution.
But ad hoc subbing of production operatives with executives is a band-aid at best. If a sustainable solution cannot be devised, Malaysia’s ranking as the world’s sixth largest exporter of semiconductors and integrated circuits as of 2021 could nosedive.
The labour shortage could also halt the momentum of electrical and electronics (E&E) exports, which rose by 18% from RM386 billion in 2020 to RM456 billion in 2021, generated 56% of Malaysia’s 2021 trade surplus, and accounted for 6.3% of 2021’s total worldwide E&E exports.
Compounding their labour woes, manufacturers are operating below capacity amid swelling global demand and chip shortages and, unfortunately, leaving big money on the table, agreed analysts and business association representatives.
“While the country’s sterling export performance suggests that the manpower shortage has no material impact on production, the more likely effect is foregone opportunities to ramp up capacity to meet increased international orders,” pointed out economist Yeah Kim Leng of Sunway University.
Industry sources have also told FMT that chipmakers were rejecting orders due to the lack of manpower, partially driven by the freeze on migrant worker intake.
Labour-linked capacity concerns could also sideline Malaysia from the global supply chain.
“Being forced to operate below capacity has resulted in delays in the delivery of goods and huge backlogs, as well as penalties being imposed on manufacturers.
“The impact could be further compounded should existing customers, given the pick-up in demand, decide to source for alternative suppliers in other countries, thus removing Malaysia from their supply chain,” warned Federation of Malaysian Manufacturers (FMM) president Soh Thian Lai.
Though the government lifted the freeze on applications to hire foreign workers on Aug 19, it will take time for foreign workers to arrive.
Further down the line, prolonged labour supply risks could deter new E&E investment and pressure existing investors to exit, denting Malaysia’s investment allure and economic sustainability.
“The labour shortage could impede Malaysia’s competitive edge as a key foreign direct investment (FDI) destination for the semiconductor global supply chain within Asean, causing Malaysia to lose out to other Asean countries,” said former Treasury deputy secretary-general Ramon Navaratnam.
As semiconductors are ubiquitous and have diverse applications, the labour conundrum also poses an inflation risk. Manpower issues could drive up the costs of intermediate and finished products such as electronic goods, digital devices and automobiles, accelerating record inflation and impacting intermediate businesses and end consumers.
Expediting foreign workers’ approval
It has been reported that Malaysia’s E&E sector needs at least 30,000 workers urgently. More will be needed if companies want to expand their factories or set up new ones.
The E&E industry in Malaysia already hosts six out of 12 of the world’s largest semiconductor companies and three out of the nine largest LED companies. The strain on resources, including the labour pipeline, will be exacerbated as new investment pours in and existing players expand operations to cater to increased international orders for chips.
In 2021 – a bumper year for FDI – the E&E sector recorded 94 approved projects worth RM148 billion slated to create 28,362 job opportunities. The question is: how will Malaysia source the human capital to staff these jobs and support the sector’s business continuity?
The best immediate solution is for the government to expedite foreign worker approvals through a transparent, predictable and effective mechanism.
“Ideally, the entire foreign worker application process should be handled online with minimal human intervention and no involvement of agents or third parties,” said FMM’s Soh.
Based on industry feedback that pinpoints the federal-level interview process as the “bottleneck”, FMM has recommended that the interview process be decentralised to individual states to effectively manage the massive volume and backlog of applications and interviews.
Otherwise, if the government drags its feet, MNCs’ business continuity, Malaysia’s coveted status as a global E&E hub, and the well-being of talents like Liew are undoubtedly in peril. - FMT
No comments:
Post a Comment
Note: Only a member of this blog may post a comment.